How Safety Sensors Are Reducing Aerial Lift Accidents
Scissor lift operators need tools to control their work environments and guard against accidents. OSHA issues hazard alerts that address the main causes of injuries and fatalities involving scissor lifts. And, the primary causes of these incidents include improper use of scissor lifts by untrained operators and a lack of modern technology like safety sensors.
What Is a Scissor Lift Safety Sensor?
A safety sensor can alert a scissor lift operator about potentially unsafe situations. For instance, a sensor can sense load on a lift. This ensures a lift operator is alerted if a lift is approaching its maximum load capacity.
Top scissor lift brands equip their models with lift sensor technology. Some scissor lift models now feature a hazardous area proximity sensor and other state-of-the-art sensors. And, construction sensor technology is constantly evolving. As companies look for ways to keep their scissor lift operators safe, sensor technology manufacturers appear poised to continue to take their safety sensors to the next level.



What Does the Future Hold for Safety Sensor Technology?
“Smart” sensors are in development. They leverage artificial intelligence (AI) and other state-of-the-art capabilities to learn. In aerial lifts, safety sensors may become available that are capable of collecting and analyzing workplace safety data. They may allow businesses to use this data to generate unprecedented workplace safety insights. In the long run, companies can leverage these insights to uncover ways to bolster aerial lift safety across their workforces. In addition, wearable safety sensors are quickly becoming a feature in many workplaces.
Wearable Safety Sensors
Wearable sensors are devices that are worn on the body and used to collect data about the wearer’s environment. They can be used to monitor things like heart rate, body temperature, and oxygen levels. While they were originally developed for use in the medical field, they are now being used in a variety of industries, including manufacturing and construction. In the workplace, wearable sensors can be used to monitor employee fatigue, stress levels, and exposure to hazardous materials. By collecting this data, employers can make changes to improve safety in the workplace.
One way that wearable sensors are being used to promote safety in the workplace is by monitoring employee fatigue levels. Workers who are tired are more likely to make mistakes that could lead to accidents. By using wearable sensors to monitor employee fatigue levels, employers can make changes to shift schedules or provide breaks when needed to reduce the risk of accidents.
Wearable sensors can also be used to monitor stress levels. Employees who are under a lot of stress are more likely to make mistakes or have accidents. By using wearable sensors to monitor stress levels, employers can take steps to reduce stress in the workplace by providing resources like counseling or relaxation rooms.
Finally, wearable sensors can be used to monitor exposure to hazardous materials. This is especially important in industries like construction and manufacturing where employees may be exposed to harmful chemicals or dust particles. By using wearable sensors to monitor exposure, employers can take steps to protect employees by providing personal protective equipment or changing work processes.
Wearable safety sensors are already making waves in industrial workplaces. These devices are worn on PPE to record worker heart rate, fatigue, body position, and hazards in the environment. While not exactly mainstream yet, the technology will no doubt be implemented across industries in years to come. For instance, safety managers could use data leveraged from fatigue-monitoring construction sensors over the course of a few weeks. With this information, managers can predict the times of day when workers are more likely to be fatigued and suffer injuries. This allows them to implement preventative measures like adding breaks to reduce the risk of fatigue.
Do You Need to Use a Scissor Lift That Has a Safety Sensor?
There is a standard load lift sensor construction requirement for mobile elevating work platforms (MEWPs). This standard was established by the American National Standards Institute (ANSI) in 2019. It requires MEWPs to be equipped with a sensor that can detect load weights and alert operators accordingly.
In addition, ANSI requires MEWPs to include a tilt sensor. Thanks to this sensor, operators can minimize their risk of tip-overs and other accidents on unsafe slopes.
Beyond these standards, no other requirements are in place for safety sensors on aerial lifts. Regardless, it is paramount for employers to do their part to provide their aerial lift operators with proper workplace safety equipment.
Scissor Lift Accidents Highlight the Value of Safety Sensors
Safety sensors can help stop a scissor lift accident. To understand why, let’s consider two recent scissor lift accidents.
A scissor lift operator at a hospital was once crushed by a concrete slab. Following the accident, it was reported that the incident could have been avoided if proximity safety sensors were installed on the lift. In this instance, the operator would have been alerted that he was getting too close to the overhead concrete, and he could have lowered himself to safety. However, proper measures were not taken on this particular worksite and on the scissor lifts used there.
Within a few years of the aforementioned accident, another scissor lift operator was killed in a similar manner. This operator was crushed while operating a scissor lift on the same worksite. Lift sensors could have protected the operator who was working on an elevated platform by warning him of the ill-fated crushing hazard.
The role of sensors in construction is still evolving. While there’s no denying the usefulness of this technology, some companies may be slow to adapt to new safety standards. Indeed, it may take a regulatory body like OSHA to require the use of these sensors to ensure they’re actually used as intended. When budgets are tights and accidents are seen as avoidable, many managers struggle to justify the investment of new technology. Still, the tide is turning, and a decade from now, we may wonder how we ever worked without safety sensors in place.
How to Use Safety Sensors to Improve Workplace Safety
The first step for making scissor lifts safer is to install certain lift safety sensors on the equipment to detect and warn workers of unsafe situations. These potential hazards include elevating the lift too high and getting too close to fixed objects. Here are a few construction sensors all scissor lift manufacturers should install on their equipment to help prevent accidents like the two described above:
✓ Height Monitoring Sensor.
This device would sensor the height of the scissor lift and alert the operator when it is in close proximity to a potentially hazardous object. This sensor can help prevent crushing accidents.
✓ Hydraulic Pressure Monitoring and Regulating Sensor.
This tool is compact and durable to regulate scissor lift pressure and is placed on the bottom platform of the lift. This construction sensor is designed to help prevent accidents caused by scissor lift malfunctions.
✓ Wheel-to-Ground Contact Monitoring Sensor.
This safety sensor can be placed on the side of the bottom platform in between the four wheels of a scissor lift. It can detect when a scissor lift is on unstable ground and faces a high risk of tipping over. This sensor can help prevent falling accidents caused by tip-overs.
In addition to high-tech lift sensors, there are a few other low-tech safety solutions for scissor lift and aerial lift operators: toolboxes and tool trays.
How Toolboxes and Tool Trays Can Improve Workplace Safety
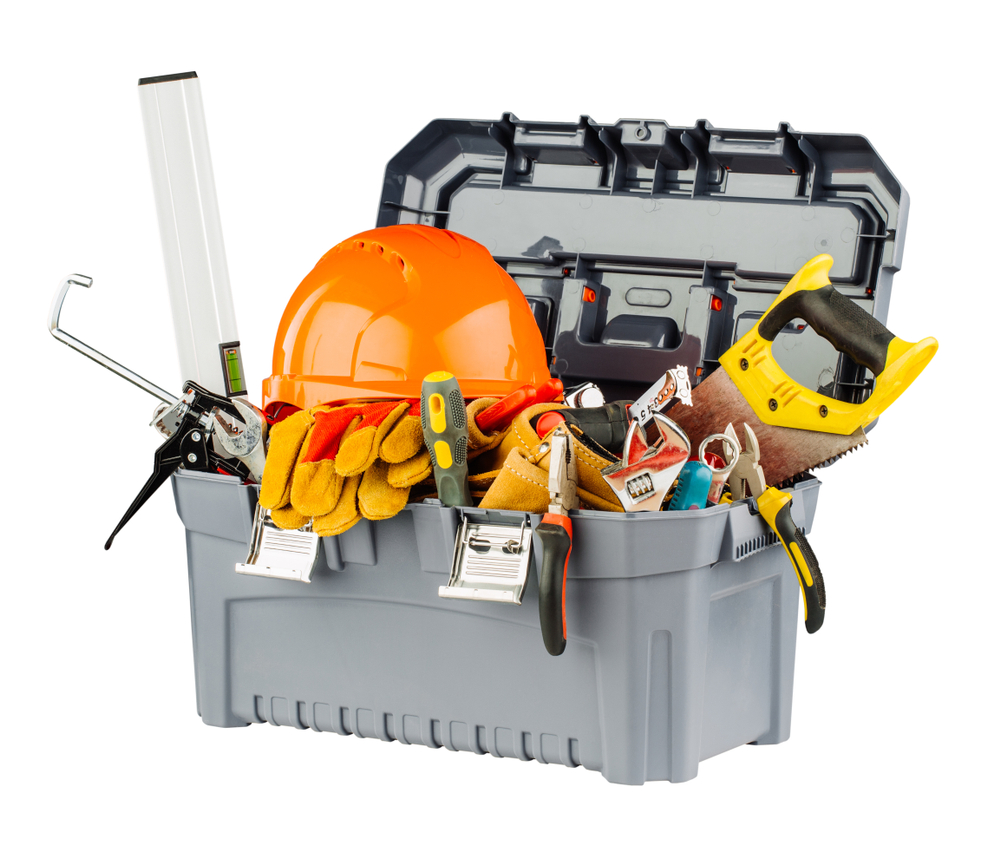
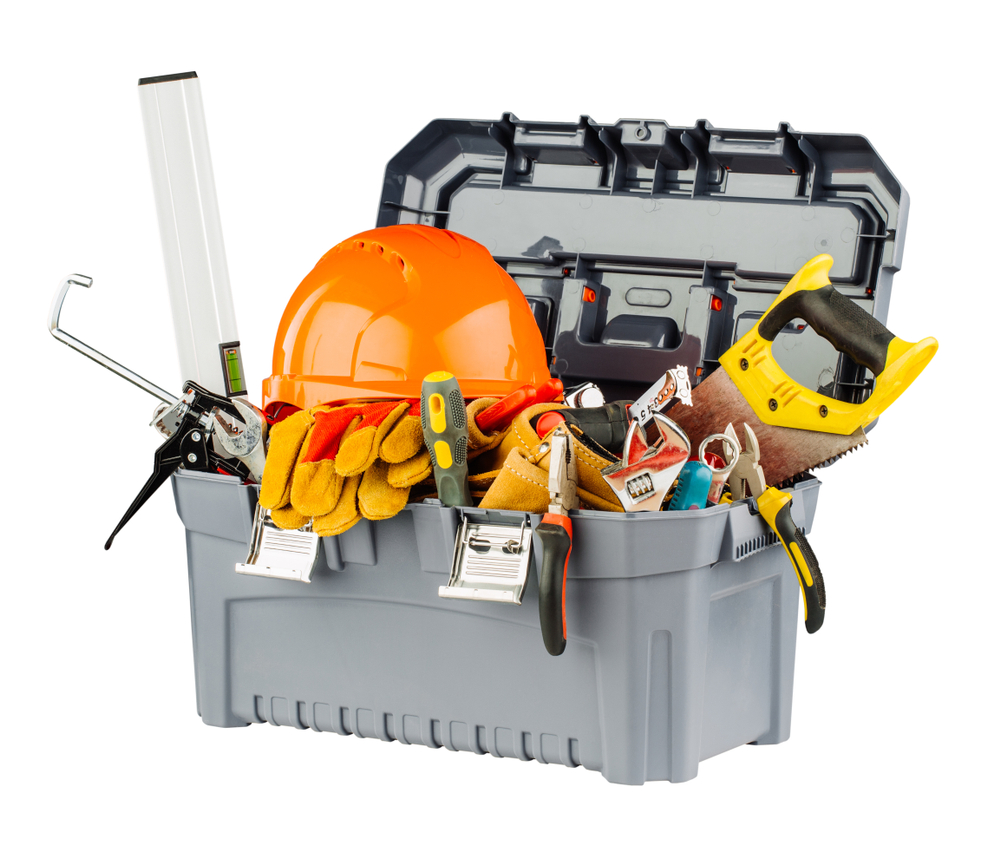
Along with lift construction sensors, tool trays play an important role in improving safety conditions with aerial lifts, scissor lifts, and all aerial work platforms (AWPs). Think about falling object hazards for a minute and a lift worker who is high up in the air and mishandles a wrench screwdriver. At any moment, the screwdriver can create a serious safety hazard. Because, if the tool hits a worker on the ground, serious injury or death could occur. That’s why scissor lift tool tray and scissor lift toolboxes are so important. And ultimately, staying organized on any AWP creates safe working conditions for workers on the ground.
Here are tips for using scissor lift tool trays and scissor lift toolboxes. Ensure your tools are on hand before going up to prevent unnecessary trips up and down, thus reducing hazards. Have one tool out of a scissor lift tool tray at a time to keep your AWP clutter-free in no time. An organized tool box or tool tray eliminates confusion and also increases productivity.
Smart, strategic placement of your scissor lift or aerial lift really helps here. Many accidents are caused by taking tools out of a scissor lift toolbox or aerial lift tool tray, reaching over the platform edge, and accidentally dropping a tool.
What Can Scissor Lift Operators Do to Minimize Risk?
Proper operation and maintenance of scissor lifts can go a long way to reduce accidents. Workers are responsible for using scissor lifts as intended – regardless of whether the machine features safety sensors or not. Appropriate workplace safety gear can also make a big difference. Reporting accidents and hazards can help workers protect themselves and their colleagues.
Fail to prioritize construction sensors and their feedback, and you could compromise the safety of your entire jobsite. OSHA violations may result in expensive fines and penalties, too. Thankfully, certification training can help scissor lift operators comply with OSHA mandates with ease.



Reap the Benefits of Best-in-Class Scissor Lift Safety Training
If you’re a scissor lift operator, be proactive in guarding against workplace accidents and injuries. By working only on equipment with safety sensors, you’ll be far less likely to be hurt on the job. Of course, education can also go a long way in preventing injuries. OSHA-compliant scissor lift certification can teach you how to operate a scissor lift properly, identify potential safety hazards, understand OSHA-issued protocols and procedures, and inspect the equipment.
ALC offers OSHA-approved certification training courses for scissor lifts and other types of aerial lifts. To learn more or register your workers, reach out online or call us today at (888) 278-8896.